As battery technology progresses to address modern applications' diverse and expanding demands, the focus intensifies on optimizing battery lifespan, charging speed, and overall performance. This development hinges on the battery chemistries and cell formats, which are crucial for manufacturers aiming to balance these factors effectively.
Battery Chemistries
The three most common cathode compositions in electric vehicles are Nickel Manganese Cobalt Oxide (NMC), Lithium Iron Phosphate (LFP), and Nickel Cobalt Aluminum Oxide (NCA), each offering advantages and challenges in the market. Several vital criteria come into play to determine a battery's suitability for various applications. These include:
Specific Energy
This measures how much energy a battery can store relative to its weight, indicating how long a battery can power a device before recharging.
Cost
The cost of manufacturing and purchasing the battery impacts its affordability for consumers and manufacturers.
Lifespan
How many charge and discharge cycles a battery can undergo before its performance significantly degrades.
Performance
The battery's efficiency and stability under different conditions, such as temperatures and loads.
Safety
The risk of the battery overheating, catching fire, or experiencing other failures.
Specific Power
The battery's ability to deliver high power outputs is essential for applications requiring quick bursts of energy, like accelerating a vehicle.
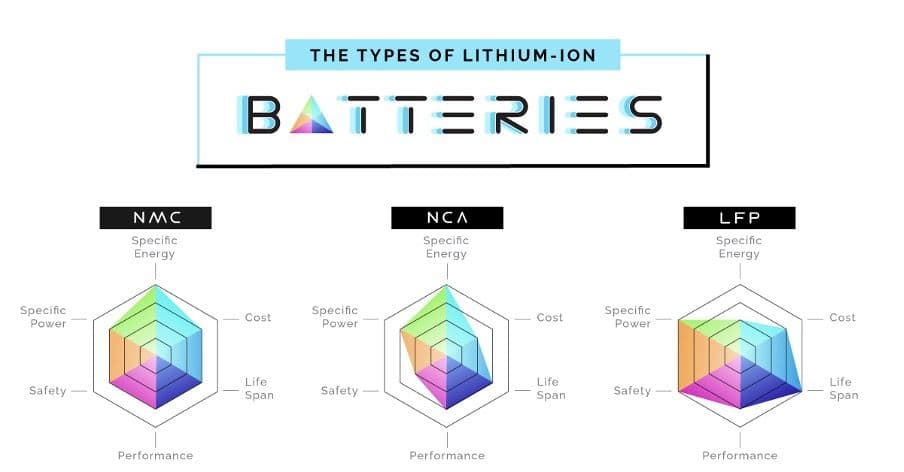
Types of Lithium-Ion Batteries – Visual Capitalist
Lithium Nickel Manganese Cobalt Oxide (NMC)
Lithium Nickel Manganese Cobalt Oxide (NMC) batteries have become a crucial component in the electric vehicle (EV) industry, dominating a 60% market share due to their exceptional energy density and performance. These highly adaptable batteries, with varying compositions, such as NMC 622 or NMC 811, allow for nickel, manganese, and cobalt ratio adjustments. They are widely used across different transportation modes, from urban electric vehicles to e-bikes and electric motorcycles, highlighting their versatility and significance in the shift to cleaner energy.
The sourcing of materials, especially cobalt, presents significant ethical and geopolitical challenges. As a result, the battery industry is working to decrease reliance on such controversial materials. This effort has resulted in new approaches to reduce cobalt content. Companies like Tesla are shifting towards nickel-rich alternatives, which could potentially reshape NMC battery chemistry for better sustainability. EV manufacturers such as Polestar, BMW, and Volvo also use NMC batteries in their electric vehicles.
Asia's dominance in NMC adoption, driven by its substantial EV market, sets a precedent that could shape global market trends. With ongoing research dedicated to refining NMC battery technology, the future promises further advancements in composition, recycling practices, and overall sustainability, ensuring their continued relevance in the evolving energy storage market.
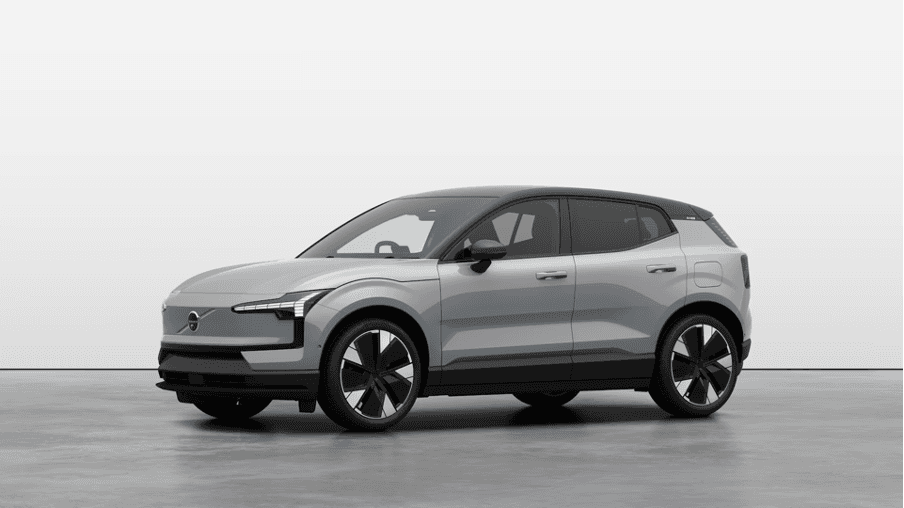
Volvo EX30 – Volvo
Lithium Iron Phosphate (LFP)
Lithium Iron Phosphate (LFP) batteries, which claim nearly a 30% market share, are distinguished for their safety and eco-friendliness and are gaining significant traction, particularly in China. These batteries are primarily utilized in light electric vehicles, energy storage systems, and portable electronics, where safety and longevity are paramount. The lower risk of thermal runaway and the absence of toxic materials make LFP an ideal choice for applications requiring stringent safety standards.
Market dynamics driving LFP adoption include its cost-effectiveness over the battery's lifecycle, despite a higher initial cost than some alternatives. The growing emphasis on renewable energy integration and the need for reliable energy storage solutions further strengthens its market position. The industry has seen a shift toward LFP chemistries, with geographical expansion in Europe and North America, influenced by regulatory policies promoting clean energy and sustainable battery solutions. BYD, a battery cell and EV manufacturer uses LFP in several of their EV models; Tesla has also used the chemistry in the Model Y and Model 3 rear-wheel drive cars.
Material sourcing for LFP batteries is relatively more sustainable than other cathode compositions. Iron and phosphate's abundance and lower toxicity reduce environmental and health concerns. Additionally, the straightforward recycling process of LFP batteries aligns with global efforts to promote a circular economy in the battery industry, further enhancing the sustainability profile of the cathode composition.
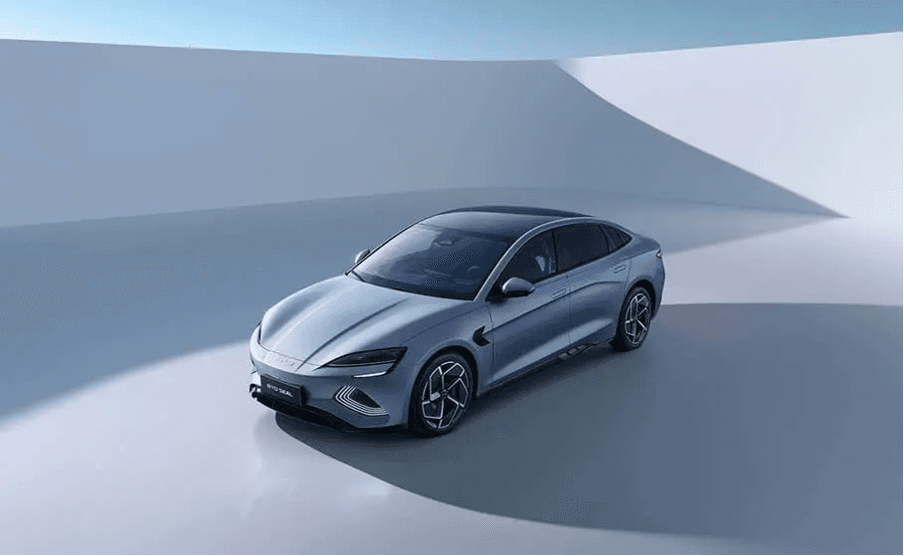
BYD Seal – BYD
Lithium Nickel Cobalt Aluminum Oxide (NCA)
Lithium Nickel Cobalt Aluminum Oxide (NCA) batteries, holding an 8% market share, are integral to the high-end EV sector, particularly for long-range models like those from Tesla, due to their impressive energy density. Beyond EVs, NCA batteries are used in consumer electronics, providing power and longevity for devices like laptops and smartphones. The energy storage sector also benefits from NCA's high energy density, utilizing these batteries in systems that require compact yet powerful solutions.
Various factors shape the market dynamics for NCA batteries, including consumer preferences for longer-range EVs and more durable consumer electronics. The geographical adoption of NCA technology varies, with North America and Europe leading in premium EV usage. However, Asia is also a significant player, not just in consumption but in the manufacturing and development of NCA batteries, driven by market demands and local manufacturing capabilities. NCA batteries can be found in the Audi Q8 e-tron and older Tesla models, such as models X, S, and 3.
Material sourcing for NCA batteries, particularly nickel and cobalt, raises sustainability and ethical concerns. The industry is increasingly focused on responsible sourcing practices and exploring ways to reduce the reliance on these materials. This shift not only addresses ethical concerns but also aims to enhance the sustainability of NCA batteries, ensuring their long-term viability in the market.
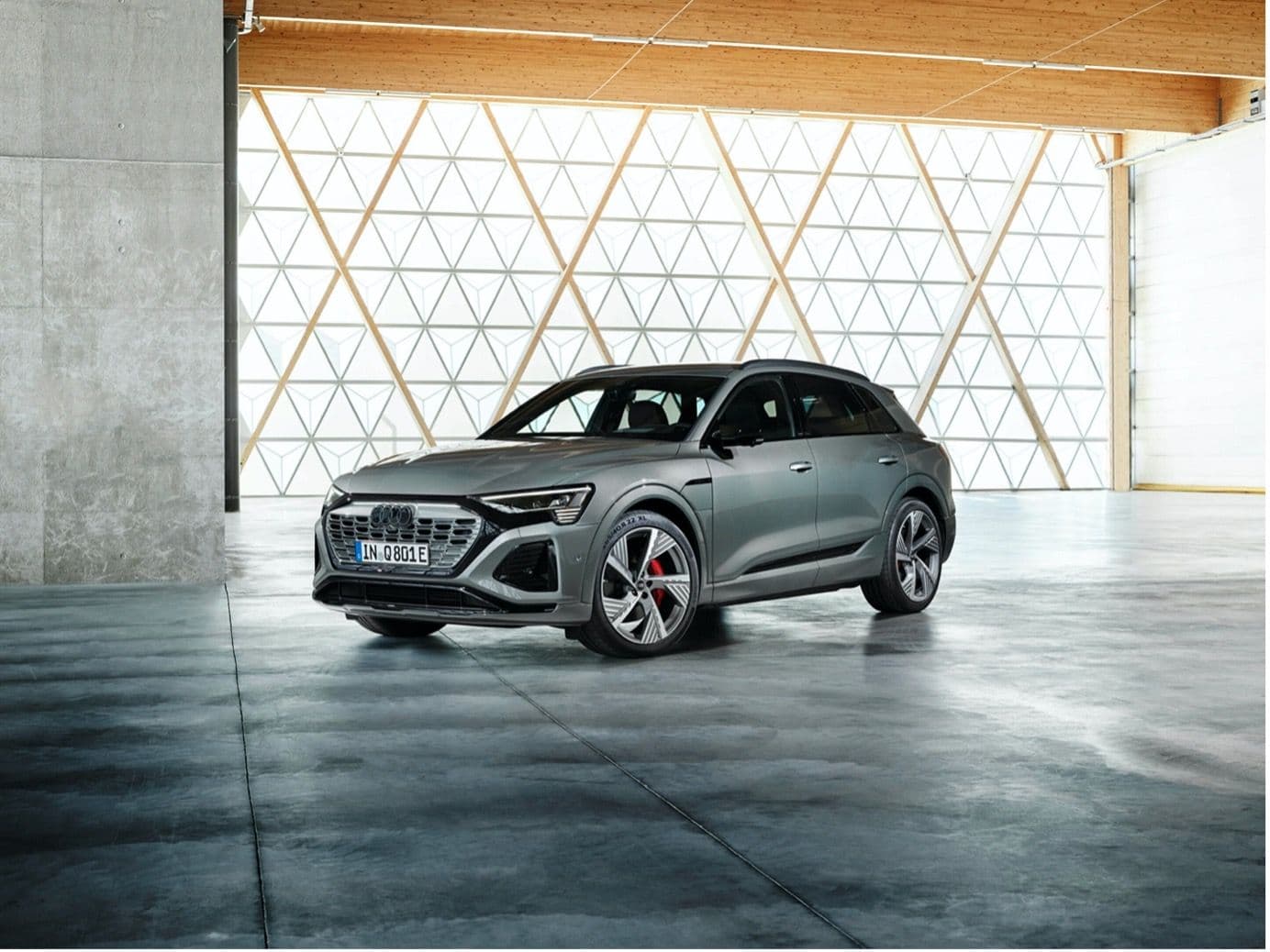
Audi Q8 e-tron
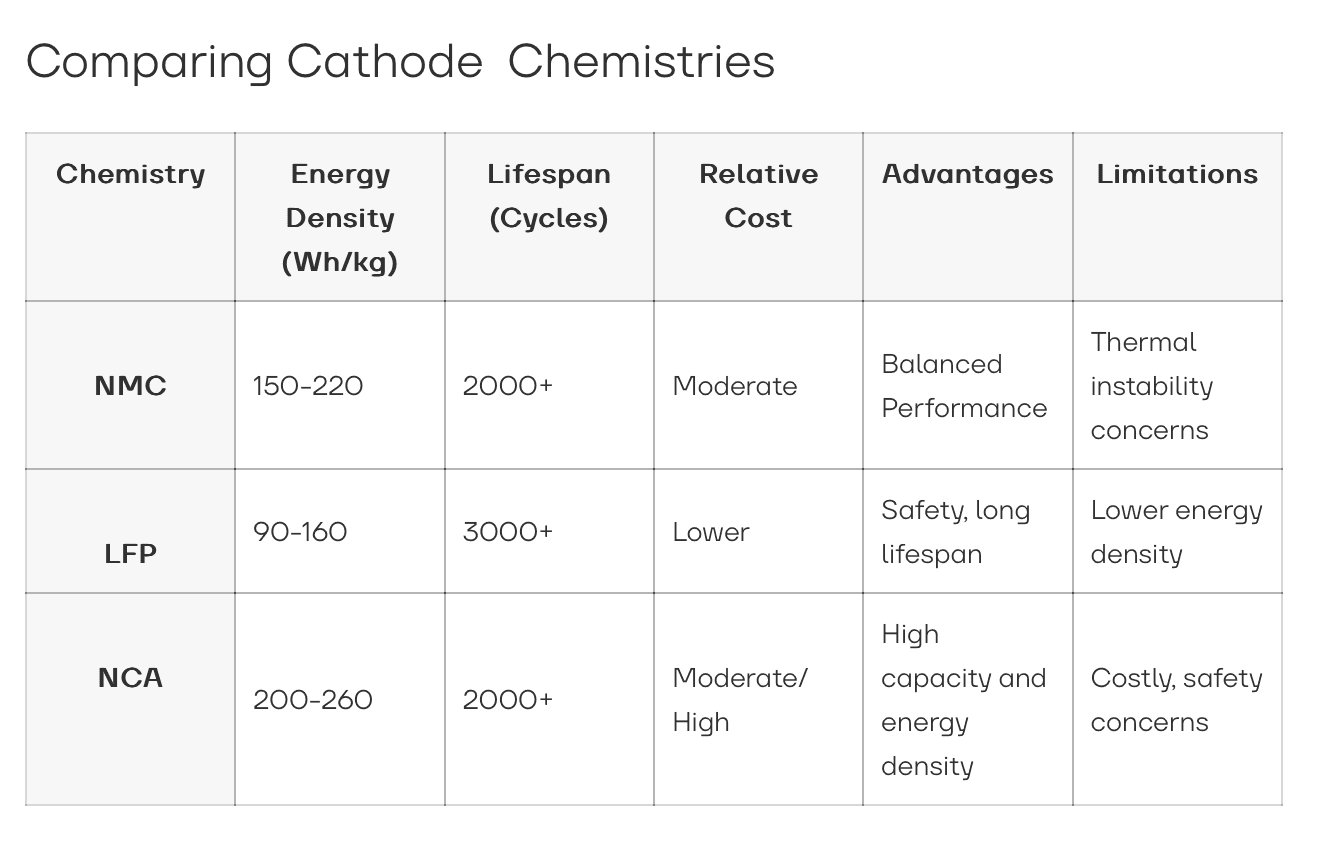
Cell Formats
Another critical aspect of lithium-ion batteries is the variety of cell formats available, each with unique characteristics and applications. The three most common are cylindrical, prismatic, and pouch cells.
Cylindrical
Initially developed for consumer electronics, cylindrical cells have become prevalent in electric vehicles. The 2170 cell, measuring 21mm by 70mm, is especially popular, produced by companies like Panasonic Energy and Tesla. These cells consist of an anode, a cathode, and a separator rolled into a cylinder with electrolyte and are cost-effective to produce due to established manufacturing techniques. Although their round shape can reduce energy density in EV battery packs, their mechanical robustness and enhanced energy density keep them favored in the market.
Prismatic
Contrary to its name, a prismatic cell is box-like, with its battery layers stacked and compressed within a rigid casing. Mainly produced in Asia by companies like CATL, these cells are often favored for lithium iron phosphate (LFP) chemistries. Given their thickness and rigidity, prismatic cells are larger and more expensive to manufacture than their cylindrical counterparts due to their complex assembly and the need for more materials. However, they offer advantages like higher power capacity and improved energy storage, driving their rising popularity, especially in electric vehicles. The prismatic cell's design allows space-efficient assembly in battery packs, enhancing overall efficiency. One of the challenges with prismatic cells is their heat management during fast charging caused by the tight packing, compared to cylindrical cells, where the metal casing and looser packing facilitate a better cooling capacity.
Pouch
Pouch cells stand out with their flexible "bag" design, allowing for various sizes and efficient space utilization. Their construction involves stacking the anode, separator, and cathode layers inside a flexible laminate pouch, typically combining aluminum and plastic. This lack of a rigid casing contributes to their high energy density and low manufacturing costs as they are comprised of affordable materials and have a straightforward design, simplifying production.
However, the soft casing of pouch cells introduces potential drawbacks, such as vulnerability to damage, which can pose safety risks. In EV applications, this requires protective measures like a more robust module structure, which can minimize the energy density benefits. Companies like SK Innovation manufacture pouch cells and supply them to major automotive manufacturers, including Ford and Mercedes-Benz.
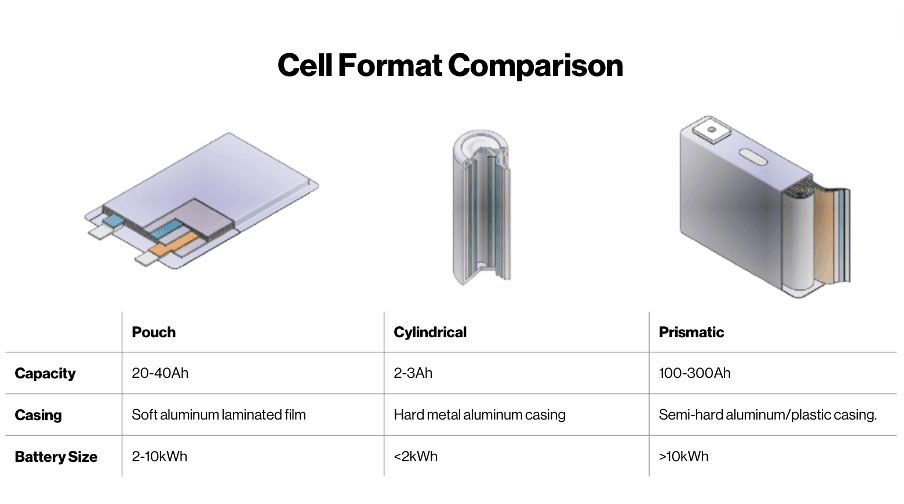
Emerging Trends and Innovations
According to a recent study by Addionics, market analysis indicates a diverse preference for cell formats:
- Prismatic cells currently hold around 40% of the market.
- Pouch cells are close to about 35%.
- Cylindrical cells account for 10%.
This variety suggests a market adapting to diverse needs, with each format finding its niche based on specific demands, with manufacturers like LG Chem and Samsung offering a range of cell formats to address different needs.
Alongside these market trends, ongoing advancements in the materials used in lithium-ion batteries exist. Innovations are leaning towards nickel-based (Ni) oxide and silicon (Si) for anodes, aiming to achieve higher energy densities and reduce manufacturing costs. Battery design is evolving to better integrate into specific applications, moving beyond traditional configurations. This approach is evident in the increasing adoption of designs like "cell to pack," the cells are integrated into the full pack instead of individual modules, optimizing space and performance.
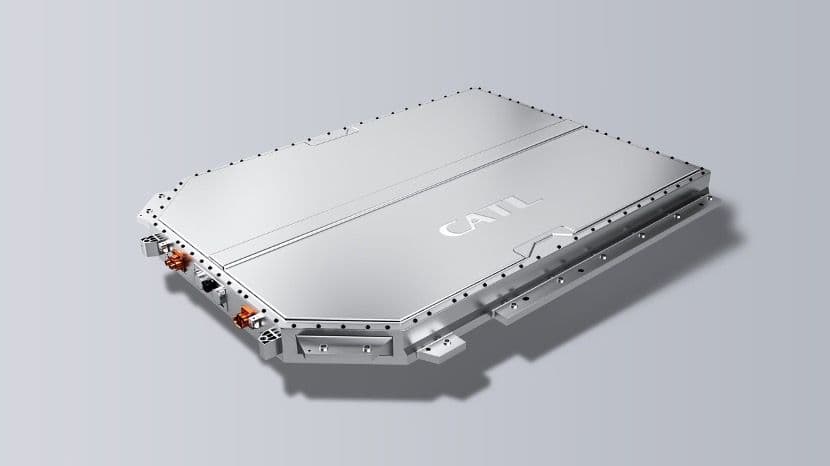
CATL's Cell-to-Pack Technology, "Qilin" – CATL
The lithium-ion battery sector is witnessing significant advancements and shifts in refining battery chemistries and diversifying cell formats.
With a shift toward more balanced cathode compositions like NMC and adaptable cell formats such as prismatic and pouch, the industry is aligning with higher efficiency and sustainability demands. As advancements continue, staying aligned and embracing innovations will be pivotal for manufacturers, consumers, and researchers.The potential for future research and development in battery technology is immense, with the possibilities of new chemistries or breakthroughs on the horizon, promising even more efficient and sustainable solutions. A crucial aspect to consider is recyclability – regardless of the cathode composition or cell format, the material in lithium-ion batteries can be recycled indefinitely, underscoring the potential for innovation and paving the way for a sustainable energy future.