In the race to reduce our carbon footprint and transition to a more sustainable energy landscape, the spotlight is on electric vehicles. Central to this transition are the batteries powering the clean energy transformation. However, these batteries rely on a complex supply chain of raw materials, and ensuring their availability and sustainability is critical.
Lithium
Lithium-ion batteries are the driving force behind our efforts to combat climate change. Their lightweight design, large energy capacity, and rechargeability make them indispensable in reducing reliance on gasoline and diesel. While lithium is present in small amounts in nearly every rock, its extraction poses challenges. It's primarily obtained by pumping lithium-soaked brine, which is then spread out in evaporation ponds, allowing the water and salt to dissipate, leaving behind lithium carbonate in powder form. This process is time-consuming, taking 12 to 18 months with multiple evaporation stages. With global reserves at around 105 million metric tons, lithium supply faces high risks due to resource scarcity and geographical concentration.
The environmental toll of lithium mining often goes unnoticed due to the growing demand. Large tracts of land are required, and billions of gallons of groundwater are consumed, leading to a high risk of environmental contamination. The construction and financing of lithium mines take a decade or more, requiring substantial investments. Australia, Chile, and China are the primary mining regions, with Australia leading the way in 2022.
To address the environmental impact of lithium mining, including the creation of large damps and holes from excavation, it's important to highlight ongoing efforts to mitigate these effects. Companies are developing sustainable lithium extraction processes, such as the selective leaching process developed by ABTC, which promises a more environmentally friendly approach. This method reduces the landscape disruption and water usage associated with traditional lithium-from-brine mining, aiming to lessen the overall environmental footprint of lithium extraction.
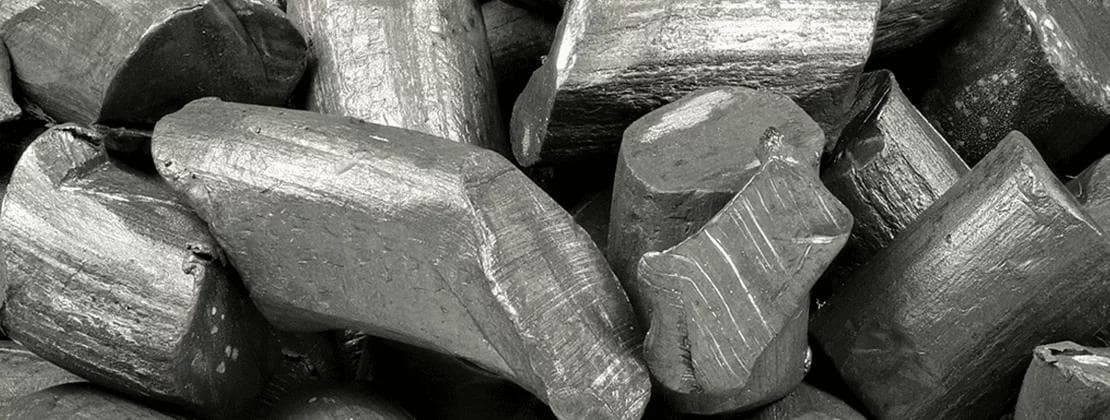
Lithium – Umicore
Carbon
Carbon, specifically graphite, plays a pivotal role in battery technology as an anode material. Graphite is crucial for battery production and is primarily found in various metamorphic and igneous rocks like quartz, granite, obsidian, and marble. The journey from extracting graphite to transforming it into high-quality anode material for batteries is laden with complex steps. After mining, the graphite flakes are meticulously processed and sorted according to size, each size serving distinct industrial purposes. Currently, the global graphite reserves stand at about 290 million metric tons, predominantly in Turkey, China, and Brazil, collectively accounting for approximately 70% of the global supply. With the demand for natural graphite steadily increasing, it is projected to exceed the available supply by around 1.2 million metric tons by 2030.
Africa's role in the graphite market is growing significantly. As of 2021, it contributed 9% to the global supply. However, the expansion of graphite mining in African regions hinges on substantial investments, support for mining activities, and assurance of the quality of anode material to satisfy the stringent requirements of the battery industry.
The battery industry is witnessing a shift towards synthetic graphite, primarily driven by technological advancements that reduce production costs and enhance capacity, making it an attractive option for battery manufacturers. This transition is also influenced by the need for more sustainable production processes, as synthetic graphite can be produced with a lower environmental footprint than natural graphite mining. CarbonScape, a startup based in New Zealand, has made a significant breakthrough in sustainable graphite. The company has recently received funding for commercializing graphite made from woodchips. This innovation provides a greener alternative to traditional graphite mining but also helps reduce the carbon footprint of EV batteries.
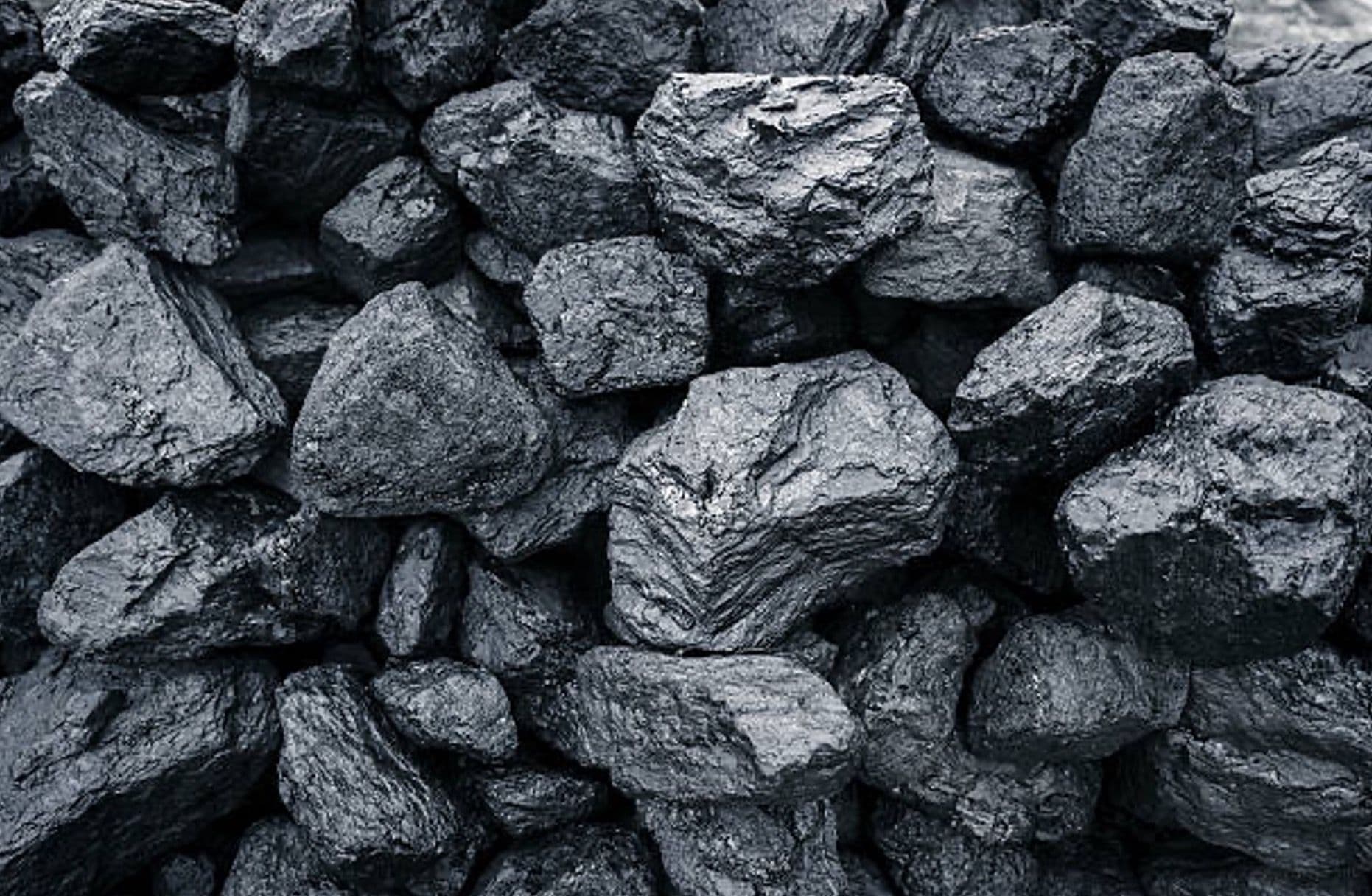
Graphite – iStock
Aluminum
Aluminum, constituting 8% of the Earth's crust, is an indispensable element in battery technology, particularly in the cathode current collector. Its primary source is bauxite, a sedimentary rock abundant in hydrated aluminum oxide. The global bauxite production exceeds 160 million metric tons each year, with significant contributions from Australia, China, Brazil, India, and Guinea. The world's bauxite reserves, estimated to be 30 billion metric tons, are spread across diverse regions, including Africa, Oceania, South America, the Caribbean, and Asia.
The aluminum supply chain faces challenges primarily due to resource allocation issues, which have led to escalating prices. However, the abundance of bauxite reserves suggests a sustainable supply for the foreseeable future, extending over several centuries.
The automotive industry is witnessing an increase in the use of aluminum, driven by the demand for lighter vehicles and the shift towards EVs. Aluminum content per vehicle has been rising steadily, with expectations for further growth as the industry continues innovating in battery electric vehicle (BEV) architectures and applying aluminum cast parts. This is exemplified by cars like Tesla's Model S, which utilizes over 800 lbs of aluminum for various components, underscoring the material's critical role in achieving lightweight, energy-efficient vehicles.
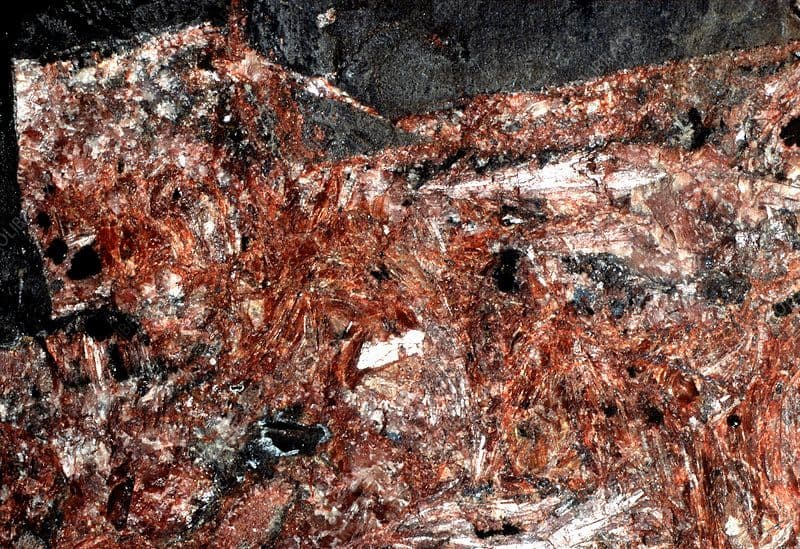
Bauxite Aluminium Ore – Science Photo Library
Manganese
Manganese, the fourth most utilized metal worldwide, predominantly serves the metallurgical sector, with less than 1%, used in battery production. Despite its minimal use in batteries, manganese plays a crucial role in the composition of cathode materials. The global manganese reserves are estimated to be around 1.9 billion metric tons. Geopolitical instability is a significant supply chain challenge for manganese, especially considering that China is responsible for exporting about 70% of the world's refined manganese. This heavy reliance on a single nation poses risks to the supply chain. Often underappreciated in the battery industry, manganese's processing capacity has not kept pace with that of other critical battery metals like lithium. This mismatch has led to an increasing gap between supply and demand for manganese.
In 2022, key manganese-producing countries included South Africa, Gabon, Australia, and China. Notably, China's manganese production experienced a temporary decline due to disruptions caused by the COVID-19 pandemic.
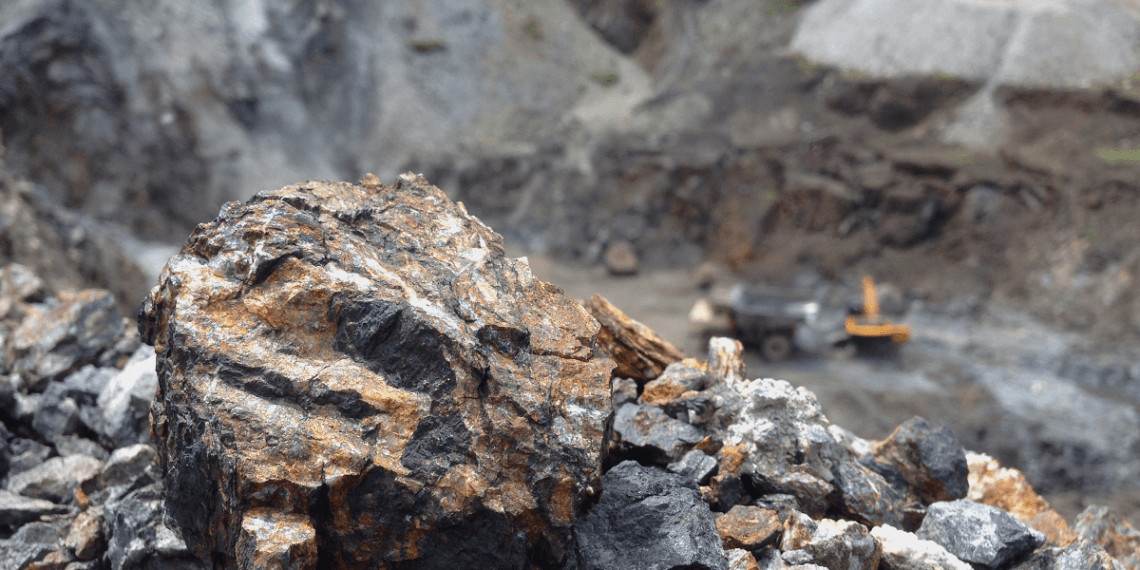
Manganese – The Assay
Cobalt
Cobalt is a critical component in the cathodes of high-energy-density lithium-ion batteries. The majority of the global cobalt supply emerges as a by-product of large-scale nickel and copper mining. While the world holds approximately 11 million metric tons of cobalt reserves, the extraction process is tainted by unethical mining practices, casting a shadow over its long-term sustainability. The Democratic Republic of Congo, a significant source of cobalt, has been particularly scrutinized for such practices.
In light of these ethical concerns, numerous EV manufacturers are actively reducing the cobalt content in their batteries. They also invest in developing alternative technologies, like cobalt-free lithium-iron-phosphate (LFP) batteries, which offer a more sustainable solution. Despite these shifts, the Democratic Republic of Congo, Indonesia, and Russia remain leading cobalt producers.
Efforts are being made to diversify the cobalt supply chain away from high-risk areas like the DRC. Australia and Canada, for example, are highlighted as countries with large cobalt reserves and strong environmental, social, and governance (ESG) ratings, offering opportunities to minimize the risks associated with cobalt's current supply chain dynamics. By turning to countries like Australia and Canada, the industry can reduce its dependency on cobalt from high-risk regions while supporting sustainable and responsible mining practices.
Copper
Given its superior electrical conductivity, copper is essential in battery technology as an anode current collector. Despite being the 25th most abundant element in Earth's crust, copper's supply chain is vulnerable to various disruptions. A significant concern is the concentration of supply sources; a major disruption at one of these sources can ripple through the entire supply chain. This was exemplified in 2021 when strikes at the Las Bambas mine in Peru led to a halt in operations for several months, illustrating the fragility of the copper supply.
Approximately 65% of the world’s copper resources are distributed between five countries: Chile, Australia, Peru, Mexico, and the United States, with Chile, Peru, the Democratic Republic of Congo, and China being the leading producers. This geographical concentration of copper resources underscores the potential risks to the global supply chain.
Recycling copper is critical to managing supply chain risks and efficiently reintroducing this valuable material into the economy without losing performance. Recycled copper demands significantly less energy than extracting new copper, thus lowering CO2 emissions. Upcoming regulations and government incentives in copper-consuming countries are promoting recycling efforts to ensure supply and decrease reliance on geographically concentrated sources.
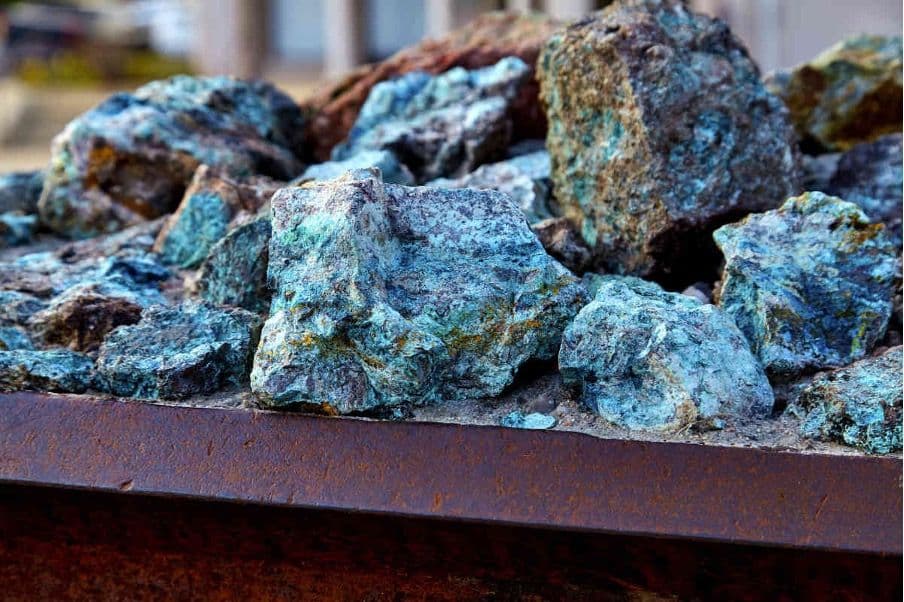
Cobalt-Copper Ore – iStock
Nickel
Nickel's role in the battery industry is set to expand significantly as it begins to replace cobalt, owing to its cost-effectiveness and a more transparent supply chain. Nickel, mined from metal ore deposits globally and even detected in meteorites, is becoming increasingly crucial in battery production. While nickel mining raises environmental concerns, particularly regarding pollution and greenhouse gas emissions, these issues are less severe than other battery metals. An important distinction in nickel mining is the extraction from sulfide deposits, which is more environmentally friendly than laterite deposits. However, it comes with higher exploration and mining costs.
As of 2022, Indonesia significantly contributed to the global nickel supply, producing 1.6 million metric tons. This supply chain concentration raises concerns about sustainability and the environmental impacts of nickel mining, including pollution and greenhouse gas emissions. Efforts to diversify nickel sources are vital for reducing reliance on single countries and mitigating ESG risks. Countries like Australia and Brazil, with substantial nickel reserves, offer opportunities to expand the global supply chain and minimize environmental and social risks associated with nickel mining.
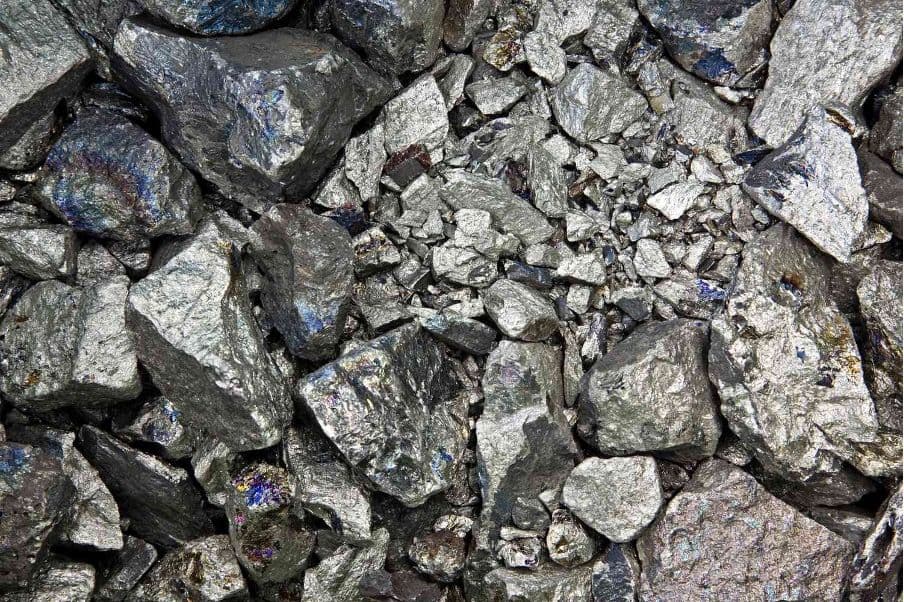
Nickel – Getty Images
Iron
While iron is not directly used in battery manufacturing, it is crucial for producing the steel that forms a key part of the infrastructure in the electric vehicle (EV) and battery industries. The supply chains for iron ore have been impacted by geopolitical issues, notably the conflict between Russia and Ukraine, both significant players in the global iron ore and steel markets. This conflict has led to disruptions and increased tensions in international trade.
The Greater Carajás Project is a significant player in the international iron ore trade in Brazil. However, it has been scrutinized for ethical issues related to the expansion of mining activities and transparency concerns, which highlight the complexities of iron ore production and trade on a global scale.
As of 2022, Australia, Brazil, and China were leading iron ore producers. Despite the challenges posed by geopolitical instabilities, the abundance of global iron reserves, estimated at around 190 billion metric tons, suggests a solid and enduring supply. This vast reserve ensures that iron will continue to support the EV and battery industries well into the future.
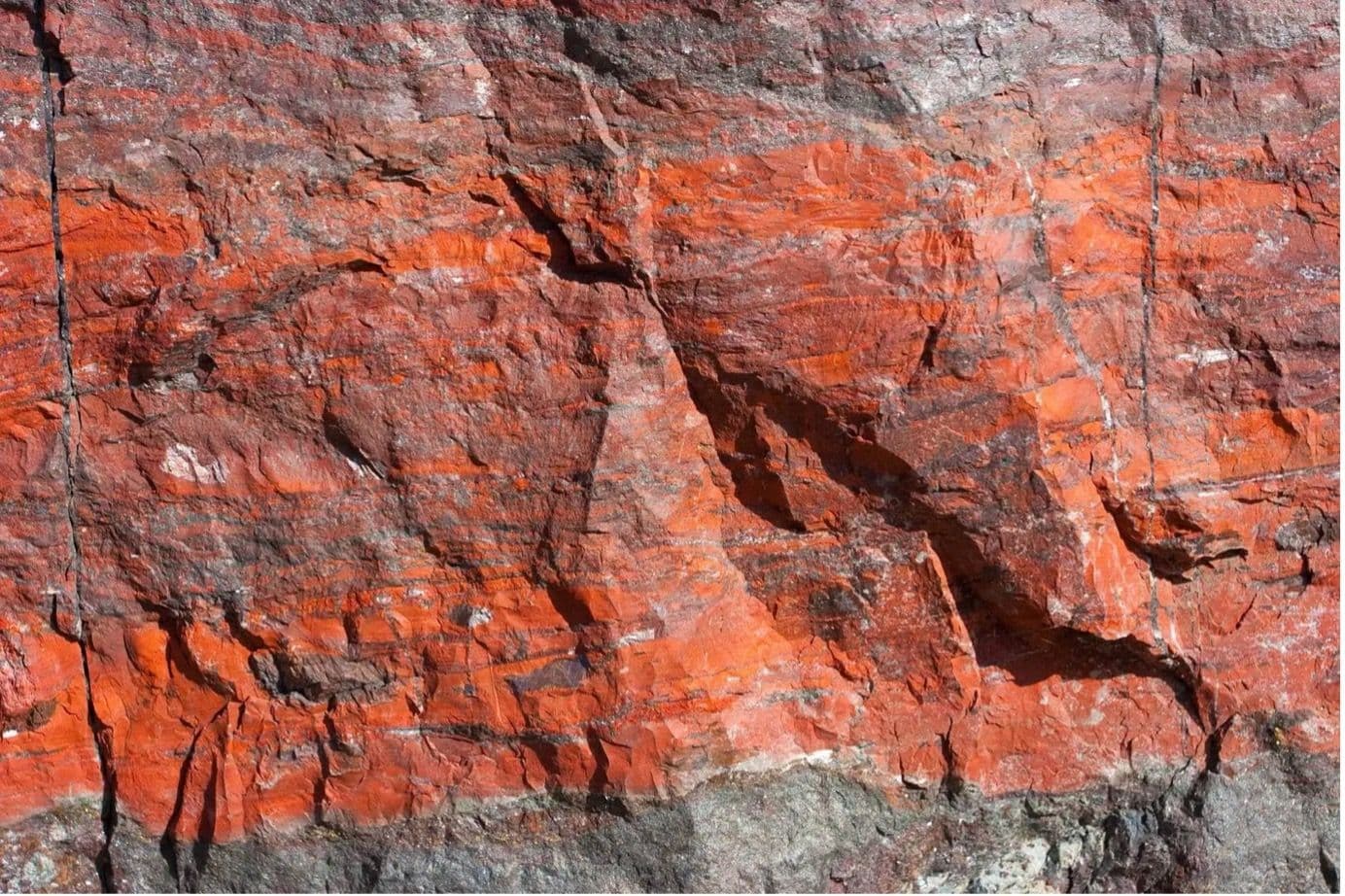
Iron Ore – iStock
Supply Chain Resilience
Creating a diverse and sustainable supply chain for battery raw materials is crucial to address the rising demand for lithium batteries and ensure energy security, economic stability, and environmental sustainability. Several global initiatives are addressing the challenges and risks of the battery raw material supply chain to ensure resilience and future sustainability:
- Global Battery Alliance (GBA) is a partnership of over 150 entities, including businesses, governments, and organizations committed to ensuring battery production supports green energy, upholds human rights, and promotes environmental sustainability. Key initiatives include the Battery Passport, sustainable sourcing of critical materials, and promoting circularity and energy access.
- EIT InnoEnergy and Demeter's €500 million fund launched the EBA Strategic Battery Materials Fund to develop a resilient and diverse battery raw material supply chain. This fund focuses on increasing EU domestic production capacities for strategic battery materials adhering to high environmental standards and the EU Battery Regulation on traceability, sustainability, and circularity. The fund also aims to diversify supply by investing in projects in EU Raw Material Partnership countries, ensuring the sustainability of the investments through high ESG standards.
- Li-Bridge, an initiative by the US Department of Energy, aims to develop a robust, sustainable lithium battery supply chain in North America to significantly increase domestic value capture, add $17 billion in direct value, and create 40,000 jobs by 2030.