Over 300 of the world's most prominent buildings, namely gigafactories, are in the pipeline to be completed and in full operation by 2030. These immense facilities, covering thousands of square kilometers, run 24 hours a day, seven days a week, to electrify our daily lives. One single factory can produce millions of batteries daily, but what does the process look like?
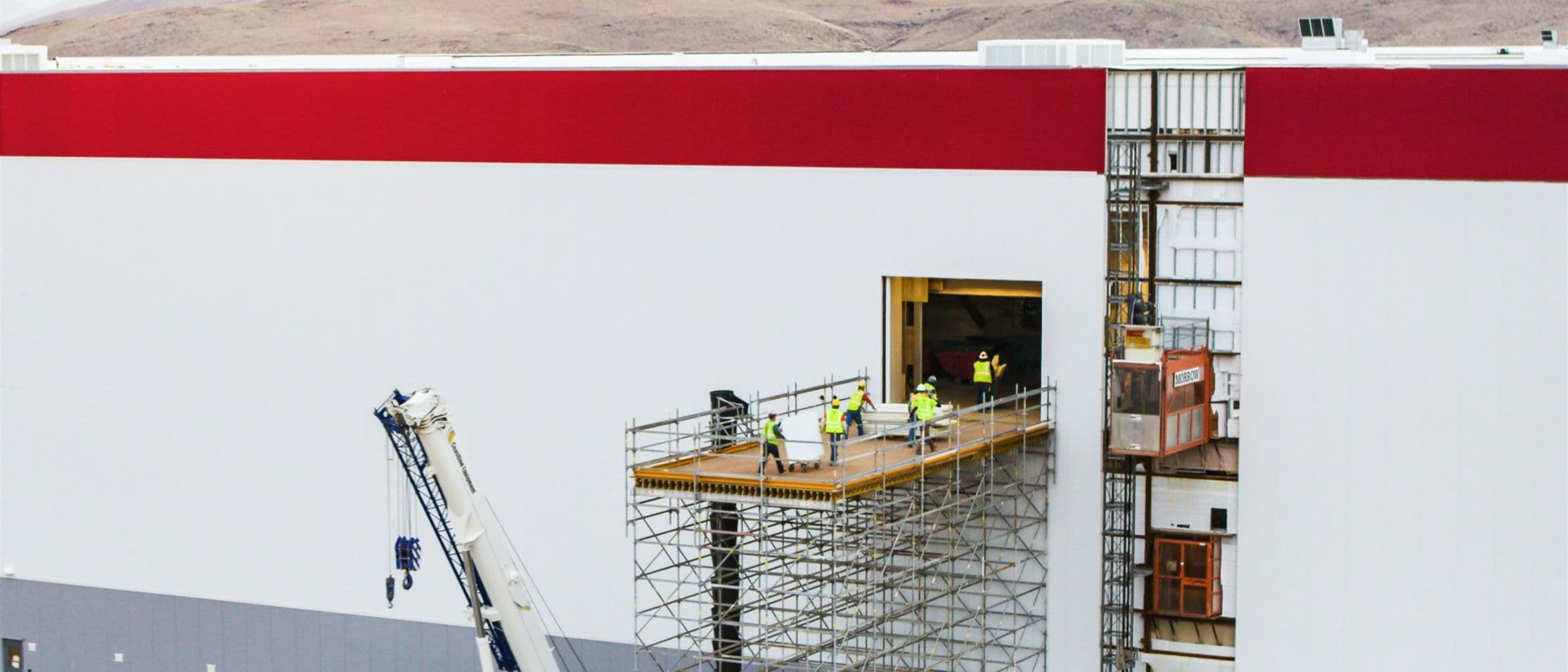
Tesla's Gigafactory in Nevada – Tesla
The battery manufacturing process within a gigafactory is complex. Due to the high production volumes and the colossal size of these factories, various challenges may arise. As a result, automation is used to integrate complex sub-processes into a unified manufacturing process. The process consists of three phases: electrode manufacturing, cell assembly, and forming, aging, and validation.
Phase One – Electrode Manufacturing
The initial step in battery manufacturing is the production of two covered layers, the anode and the cathode, called electrodes. The process uses two identical and separate production lines, one for the anode and another for the cathode, to prevent cross-contamination. Typically, the anode consists of a copper foil coated with graphite. The cathode is an aluminum foil covered with either lithium ferro phosphate (LFP), nickel manganese cobalt (NMC), or nickel cobalt aluminum (NCA). These are three of electric vehicles' six most common lithium-ion cathode technologies. Others include lithium cobalt oxide (LCO), lithium manganese oxide (LMO), and lithium titanium oxide (LTO).
Mixing
Creating a "slurry" is the initial step in the electrode manufacturing process. This is similar to mixing ingredients for a cake, where the right balance and consistency are crucial. The slurry in battery manufacturing combines powders (mainly active material), a liquid solvent, and a binder. This mixture plays a vital role in the battery's final performance, as it bonds the active material to the current collector, transferring electrochemical energy through all of the cell tabs.
Coating & Drying
After mixing, the slurry is pumped through a piping system to the coating area. The slurry is then printed on metal foil and continuously unrolled to the coating head. The coated foil then proceeds to a drying oven, evaporating the solvent and leaving the active material attached and evenly distributed. A gradual drying process is vital for obtaining high-quality electrodes, requiring ovens up to 80 meters long. The coating is applied on both sides of the foil, where the width of the printed strip determines the cell dimensions and production line capacity.
Calendaring
After drying, the coated rolls go through a finishing process called calendaring. Calendaring is where the coated rolls pass through two heated rollers, compressing the material to ensure consistent density, thickness, and optimal adherence.
Slitting
Slitting is the first cutting process to trim the foil to the size of individual electrodes required for the final assembly. The rolls from the calendaring process pass through a set of blades, cutting them into multiple smaller rolls to match the final design.
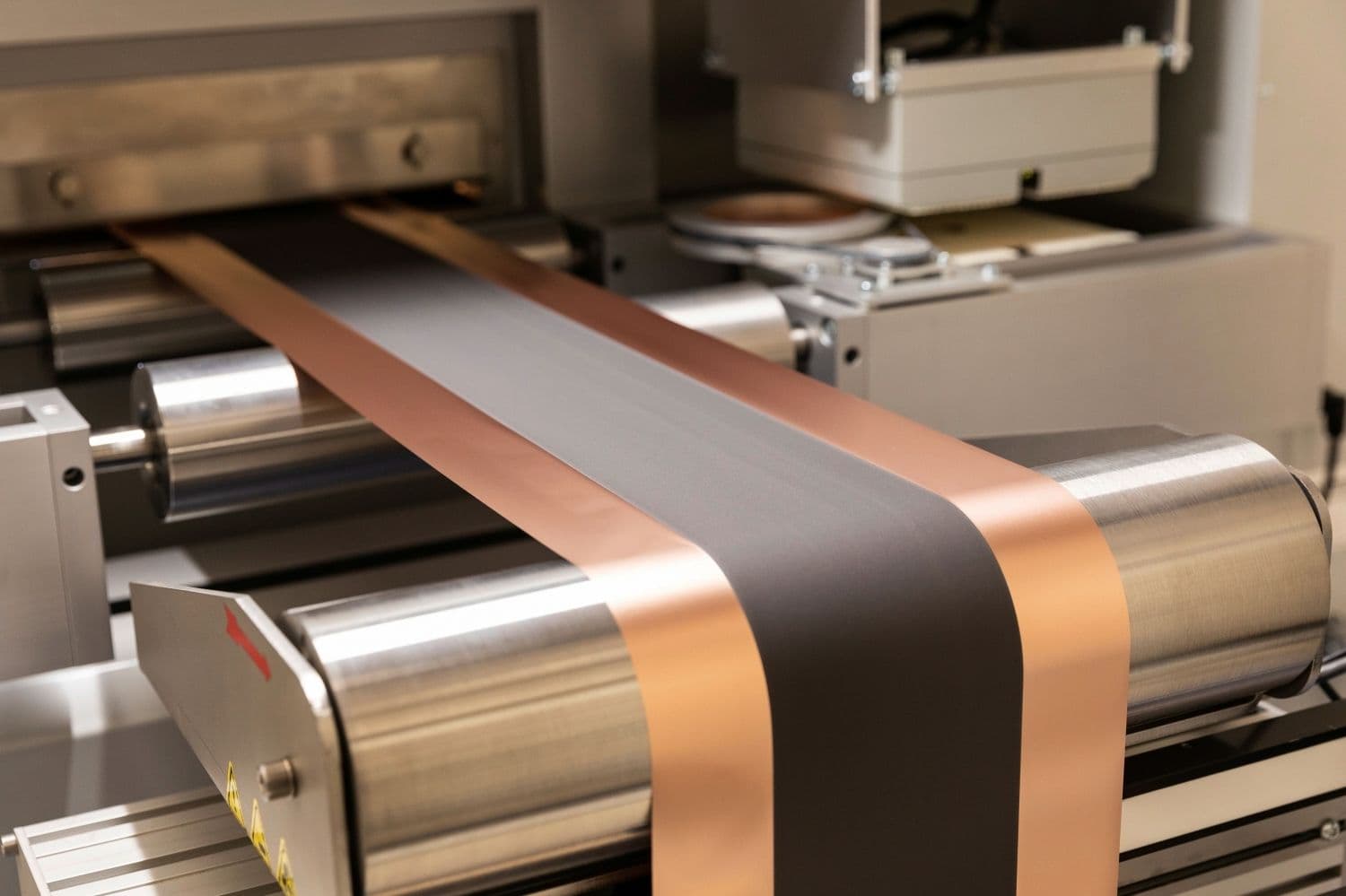
Coated and Dried Anode Foil – Volkswagen
Phase Two – Cell Assembly
After electrode manufacturing, the cell assembly process commences in specialized dry and clean rooms, which boast the strictest dew point control in any industry. These rooms are meticulously maintained at a dew point as low as -40 °C, a necessary condition to eliminate any remaining moisture to prevent battery degradation and capacity loss. Such strict environmental conditions are especially critical for moisture-sensitive chemistries like NMC811, characterized by low rates of manganese and cobalt and a high rate of nickel. In this phase, the manufactured electrodes are cut and assembled into their designated cases, with the process varying according to the specific cell format.
Notching
During notching, the coated rolls (electrodes) are cut and assembled in cases according to the cell format, the most common of which are cylindrical, prismatic, button, and pouch cell formats. The cutting machine unrolls the foil to produce individual electrode sheets, leaving uncoated areas called tabs, which become utilized during assembly.
Stacking
Once the individual sheets are produced, the electrodes undergo a stacking process. During stacking, the sheets are stacked in alternating anode, separator, and cathode layers while exposing the uncoated tabs. The two most common methods for stacking are Z-stacking and lamination.
- In Z-stacking, the separator folds over each electrode layer in a zigzag formation. Precise alignment is crucial to prevent the electrodes from extending beyond the separator, as this can lead to short circuits and increased flammability risk during cell operation.
- Lamination involves joining two components (separator/anode/separator) stacked between alternating cathode layers.
Assembly
After stacking, the electrode tabs are attached to the main terminals through welding. The cell is placed into a pre-formed packing and sealed, leaving an open edge for electrolyte filling. After vacuum sealing the remaining edge, the final product will soak for hours before conditioning to ensure proper sealing.
Phase Three – Forming, Aging, and Validation
The final stage in the battery manufacturing process is forming, aging, and validation. Conditioning is a critical stage in the process, where the cell is charged, discharged, and tested to evaluate its characteristics and performance. The cells also undergo tests such as high-temperature aging, degassing, and forming, which can take several weeks to complete.
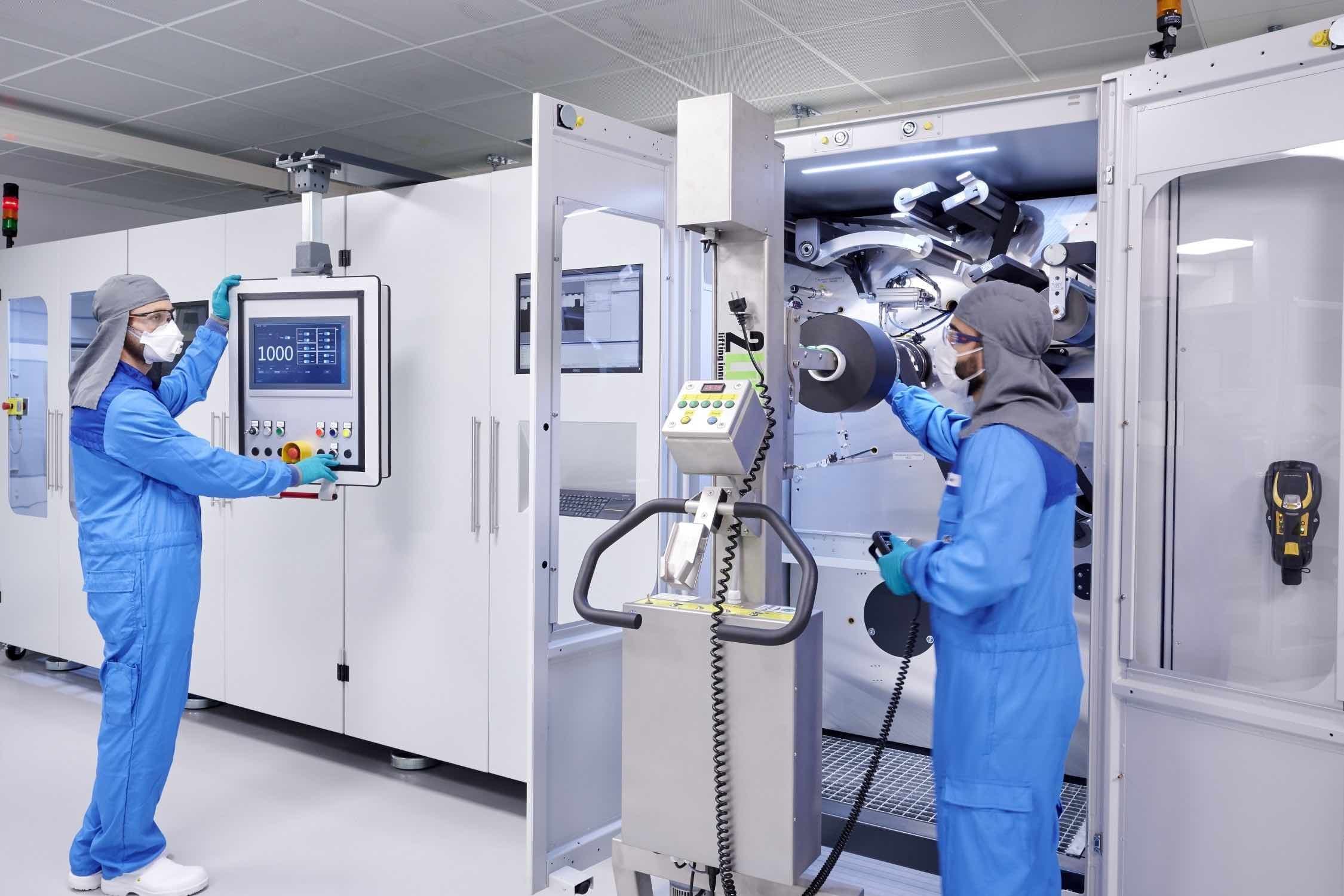
Electrode Laser Notching – BMW Group